T-FLEX CAD 中的公务机项目
在等待T-FLEX CAD 17的首映时- 该系统的制造商已准备好创建最复杂和最有趣的 3D 模型之一的材料,即公务机项目。
T-FLEX CAD 17中可用的新功能及其使用将在单独的文章中讨论。

这架飞机上的作品源于制造小型公务机的总体思路,其飞行特性与赛斯纳奖状野马和巴西航空工业公司飞鸿 100相似 ,并以纸上概念草图的形式开发。定义了外观、大致设计以及最重要的技术规格和尺寸。
直接在T-FLEX CAD中设计飞机从创建基础文件和定义通用建模策略开始。基本文件包含基本几何形状,飞机的各个部分在很大程度上取决于外部空气动力学表面。
特别是,总体战略是飞机将由几个主要部分组成:驾驶舱、机身、机翼、尾翼和发动机。每个零件都是单独建模的,但在基本几何图形中,所有零件都与基本基本文件相关联。
所以在基础文件中创建了飞机的一般轮廓。草图是使用新的样条引擎完成的,它允许您在工作时确定元素的切线,从而产生数学上“平滑”的空气动力学表面。此外,在施工线的帮助下,对框架的初步布局进行了标记。这意味着所谓的 混合参数化。

决定制作最准确的飞机外部轮廓模型,这将有助于从中切割框架元素并确保它们的正确定位。
考虑到飞机的理论横截面沿其全长变化很大,决定驾驶舱、机身和尾部外观的主要参数是几何参数。它还定义了“腹部”部分以及机身与机翼之间的连接形式。
驾驶舱的玻璃区域是使用横截面操作制成的,其中轮廓和导轨是根据指示它们与驾驶舱和机身表面相切的参数从车身突出的玻璃元件。机翼和尾翼的轮廓是使用扫掠和/或轮廓操作制作的。
平滑表面(机翼到机身的过渡等)值得特别注意。在这种情况下,应用了变量舍入操作。

由于驾驶舱、机身、机翼和尾部分别建模,基础文件应用于每个装配单元,减少了结构的总数,使尺寸关系更具可读性。
绝大多数结构元素,即框架、纵梁、大梁、肋和护板都是从实体模型中切割下来的。该模型已分为工作平面,根据标记构建并面向框架元素。主要工具是更新的 T-FLEX CAD 参考几何引擎,它允许您在定义片段的父元素更改时灵活配置片段更新。

尽管该项目除其他外包括 压制、铣削和复合框架元件,它们的建模顺序相似,即:
- 从模型中切出基体布局;
- 径向过渡(用于冲压件);
- 零件主要厚度的形成;
- 用于定位主孔和切口的平面;
- 通过切削刀具获得的底切(用于铣削零件);
- 添加或纠正先前铺设的路径,这些路径通过在片段中引用它们来定义纵梁和大梁的轮廓;
- 准确定位连接位置;
- 用辅助平面和投影标记连接器;
- 为紧固件打孔;
- 使用 T-FLEX 分析计算;
- 检查装配中的游隙和碰撞等。


这样,飞机的完整框架就创建好了。此外,还添加了连接元件(铆钉、板条等)以及支撑面板。由于适当的参数化机制 – 类似设计的接头的工作相对较快地进行,在建模过程中更改了一些参数,然后自动重建连接器以适应框架几何形状。
主要元件和机构安装在准备好的表面上,特别指定了燃料、液压、通风和防冰系统的布线。逐渐地,驾驶舱中增加了电动装置、雷达、飞行员座椅、内部镀层和内部元件以及照明设备。
机身内部以机舱、浴室、带增压泵和过滤器的耗材箱、冰箱、阀块等为模型,安装在后部,最后形成中间部分,并制作起落架使用变量预先确定的位置选项(收回、扩展等)。在工作过程中,一些安装元素在装配的背景下进行了调整,以最佳地布置主要节点。


特别注意了每个管道系统的连接点。对于飞机的每个部分,它们都预先计算并标有外部 3D 节点,例如,发动机热空气排气管 – 精确到与后部通风/除冰系统阀门的连接点部分。
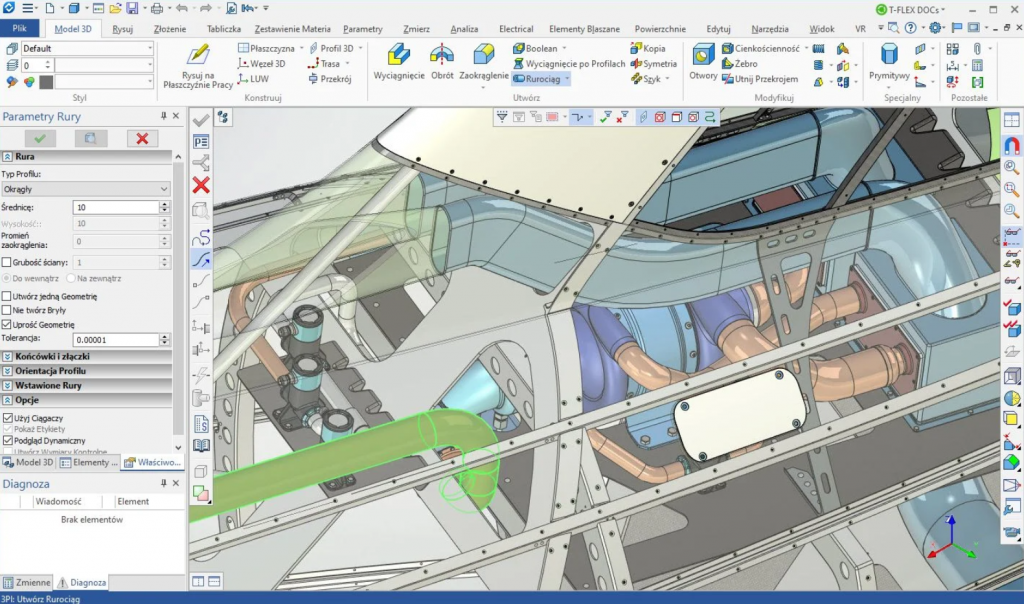
此外,还直接制作了一些管道。同时,安装了相关元件,即法兰、联轴器,例如各种类型的排水系统阀门。
所有管道工作都是在使用新的(修改后的)布线机构进行组装的情况下完成的,并且在安装支架中使用了预先准备好的节点。

创建框架后,安装主要元件并铺设管道,开始进行更详细的组装工作:安装交通灯设备(带连接点),安装各种板条、接线支架、开门机构等.
舷窗最初在船体文件中进行标记,然后投影到基本几何图形上,并在新文件组件的上下文中通过挤压从其中减去。由于照明器由“嵌套”层(玻璃、垫圈等)组成,因此使用thinness命令选项来修改布尔运算的结果就足够了,然后得到未来组装的现成碎片。然后修改碎片,减去内部体积,制作孔,分配材料等。
在大致相同的场景中,对入口门和紧急出口进行了建模。
机翼机械化建模值得特别关注。为了正确设置襟翼、副翼、方向舵 – 有必要从基本文件中正确传输计算出的安装点。然而,由于第一级机械化的所有元素也是装配体,因此首先为每个机械化单元创建一个单独的标签文件,例如安装节点从碎片通过公共标签文件作为参考几何图形移动的舱口,另一个那个舱口的元素已经被定向了,比如旋转伺服系统。结果,襟翼在准备好的环境中建模。
如果襟翼是用传统的铝棒和肋条制成的,那么方向舵和副翼是由带有特殊蜂窝填料的复合材料制成的。这种填充物的层创建如下:绘制单元草图并“乘以”线性图案,所得主体形成与舵几何形状相同的部分。

在窗扇折叠的背景下,下部窗扇面板中的众多入口舱口是使用墙壁上的轮廓投影设计的。
轮廓突起也用于通风系统的进气口设计。进气口本身的进气喷嘴是使用沿路径的扫描命令设计的- 从外壳中的开口到热交换器的法兰。
连接器分三个阶段插入飞机的每个部分,插入基本设计类型的铆钉连接器:插入节点和机构的螺栓和紧固件并覆盖固定插件。实体元件的使用不仅增加了定位紧固件的便利性,而且影响了工作速度。
所有这些活动都是针对飞机的每个部分顺序执行的,这与基本文件一致。然后驾驶舱、机身、机翼、尾翼和带框架的发动机最终组合成一个单元。


飞机的所有节点和机构,具有多个位置,堆叠在其功能层上或链接到也显示在整个组件中的变量。例如,这使得从通用单元打开舱门、延长起落架或改变皮肤颜色成为可能。

使用多种机构的便利性、高效率和工作速度以及T-FLEX CAD系统的一般功能促成了整个飞机的建造耗时约 40 周(不包括工作的发动机)又花了 6 周时间)。这架飞机的最终模型包含大约50,000 个零件。

整个发动机的详细建造,包括挂架,持续了大约 6 周。仅单个引擎就包含大约5,000个详细的建模零件。
T-FLEX CAD 图形性能和显示细节没有任何主动简化,在视频中可以观察到如此庞大而复杂的装配:




在 T-FLEX VR 中显示模型
T-FLEX VR是T-FLEX CAD的附加应用程序,可让您在虚拟空间中使用 3D 模型。重要的是要了解,用户在 VR 空间中查看的模型不是 3D CAD 模型的副本,而是同一个 3D 模型。因此,T-FLEX VR用户拥有一组独特的命令,只有在 VR 和 CAD 完全集成的情况下才能使用,例如:
- 检查机制的运作。如果 3D 组件是使用约束构建的,T-FLEX VR 用户可以在 VR 空间中“抓取”和移动设计元素,就像在现实世界中移动它们一样。在这种情况下,模拟对机构的影响,就好像将适当的力施加到零件上的选定点一样。
- 机械手– 这些是 T-FLEX CAD 3D 模型的特殊对象,可让您更改 T-FLEX CAD 变量的值,从而更改零件和装配体的几何形状。T-FLEX VR 用户可以通过相应地更改 3D 模型来重新定位这些机械手。在这种情况下,VR 是一种完全真实的设计工具,将这一过程提升到了一个新的技术水平。
- 立即激活 VR 模式。T-FLEX VR 不需要任何特殊准备来显示 3D 模型。每个模型,无论是用 T-FLEX CAD 还是其他 CAD 系统制作的模型——都可以在 VR 中显示——只需单击工具栏上的 VR 模式切换按钮。
- 基于几何的精确测量。与其他 VR 应用程序不同,T-FLEX VR 不使用多边形网格,而是使用直接几何图形。因此,用户进行的测量是 100% 准确的。您可以测量长度、直径、零件之间和到零件之间的距离…

T-FLEX VR的实际应用
与传递图形信息的传统方法相比,现代 VR 为用户提供了全新的数字模型感知水平。因此,T-FLEX VR可用于产品准备和处理的所有阶段。让我们更详细地讨论各个阶段:
- 施工和设计。设计师和工程师彻底了解产品非常重要。产品越复杂,其设计过程中犯的错误就越昂贵——更重要的是,设计师和施工人员可以尽快“现场”看到他们的工作结果。T-FLEX VR 让您可以让数字产品原型更接近设计师。
- 工业设计。外观是产品不可或缺的特征。T-FLEX VR 让您可以在短时间内评估项目。在处理大型模型时使用 T-FLEX VR 特别有用。
- 演讲和展览。如果产品尺寸很大,那么在活动和展览中展示它们的物流成本很高,或者是不可能的。在这种情况下, T-FLEX VR模块可以成为展示其广泛产品的完美解决方案。
- 员工培训和售后服务。制成品可能很昂贵或很危险。也有这样的情况,设备的生产数量很少,以至于维护人员根本没有机会在实际产品上练习他们的操作。使用 T-FLEX VR,甚至可以在产品实际制造之前进行员工培训。
